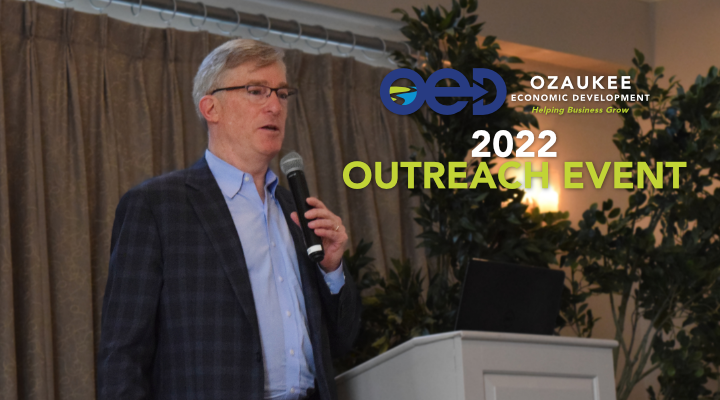
At Ozaukee Economic Development’s most recent Outreach Event, participants were treated to a presentation from our featured speaker, Blake Moret, CEO of Rockwell Automation. In which he shared some thoughtful insight into the world of Automation and how Rockwell is playing a role in helping the economy in Southeast Wisconsin thrive. Under his leadership, Rockwell integrates control and information to help make industrial companies and their people more productive and the world more sustainable. He is passionate about workforce development and creating a divers worldwide team of employees that can and want to do their best work.
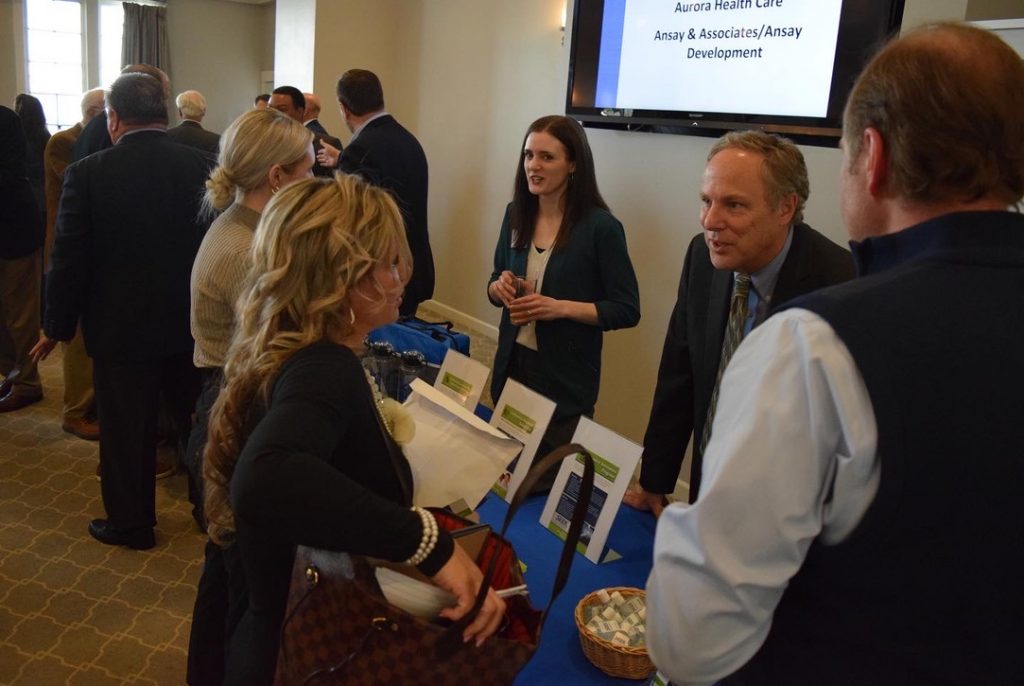
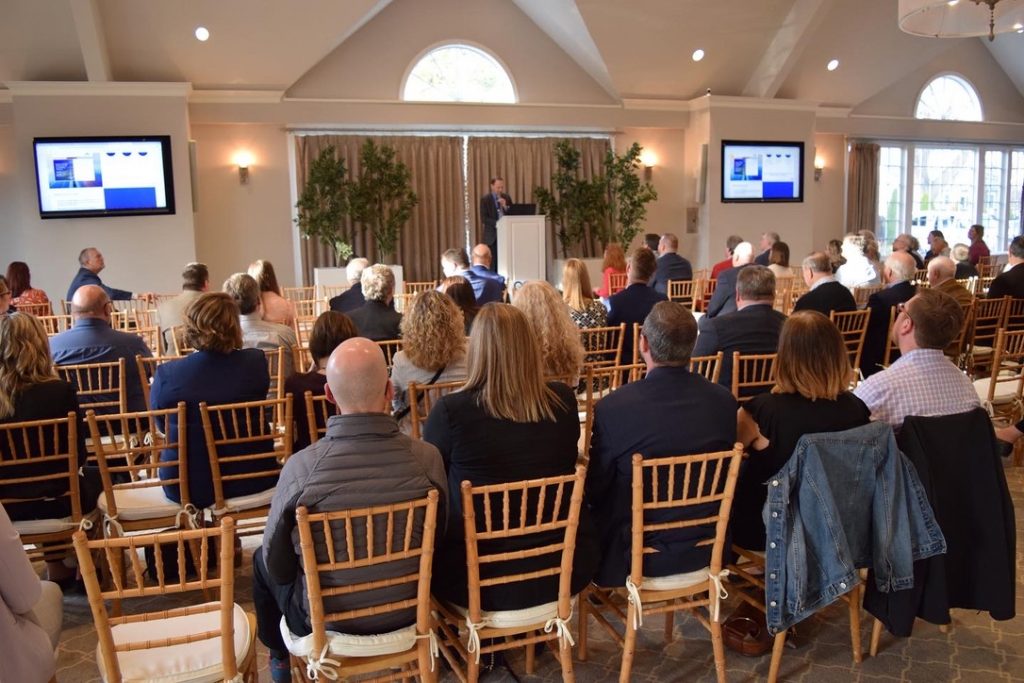
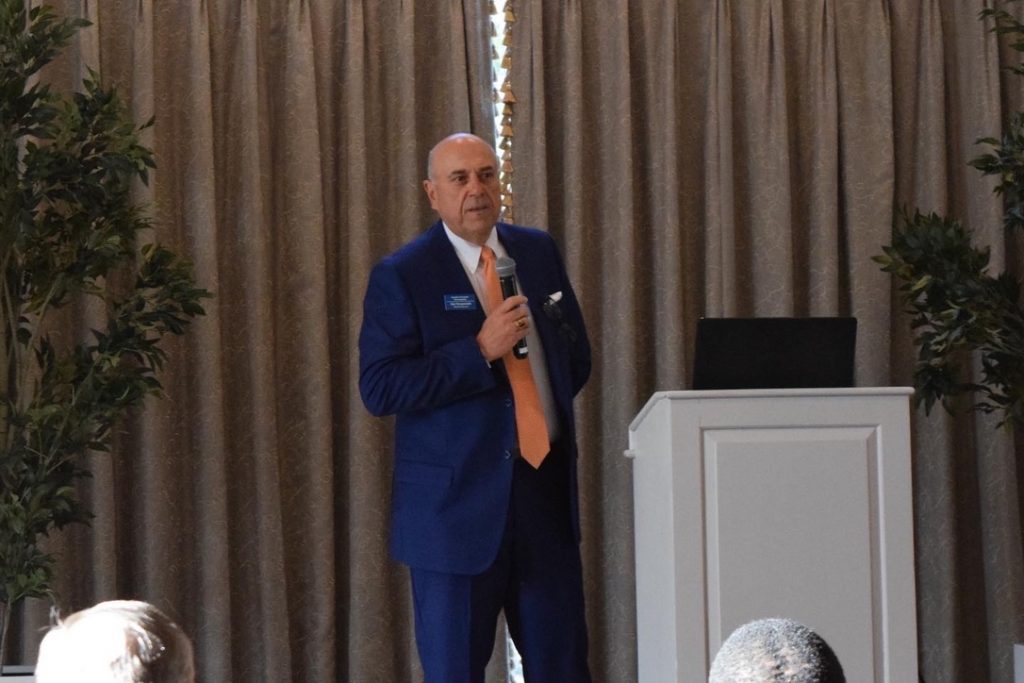
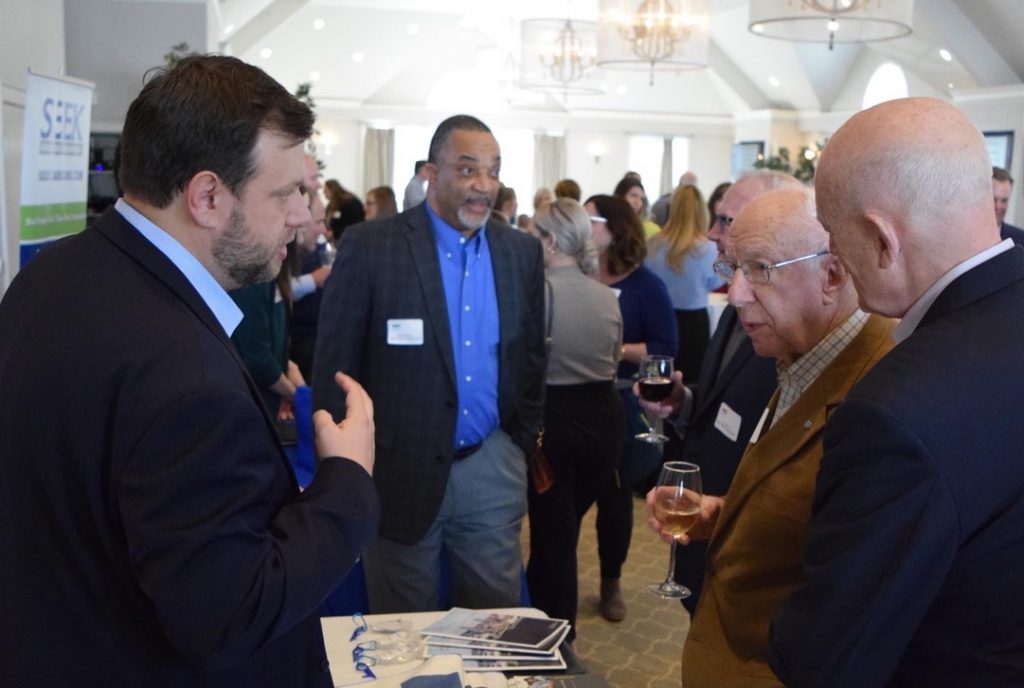
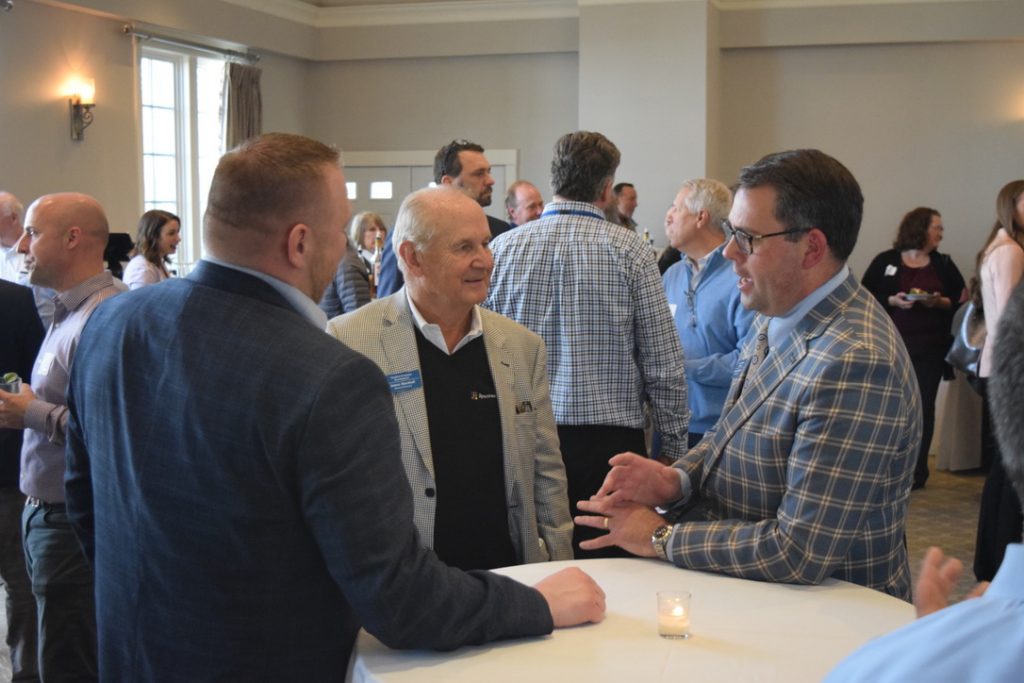

After Blake spoke to the audience, the floor was opened up to ask questions.
How do manufacturing shortages affect your company, and how does affect end users that you create products for? Is that something that you’re directly involved in as far as the manufacturer relationship?
We are keenly aware of the Intel shortages that Pat Gelsinger talked about publicly recently because we use a lot of Intel chips. If anybody read or saw our earnings release, that was the headline for us as well as our peers. The demand is unbelievable right now. All industries are trying to come out of the pandemic with new lines of business and new capacity to serve the pandemic demand. The problem is that there is a structural in the semi-conductor industry and the whole world is finding out to our dismay how fundamental semi-conductor chips are to pretty much everything that we do. You can’t produce those billions of doses of vaccines without automation and we were working with virtually all of the producers all around the world. The packaging at the end of the day needs to be done in an automated fashion. With making Electric Vehicles, it’s not just the chips that go on board. It’s about being able to produce those vehicles. You cannot produce a vehicle by hand anymore. The whole world is seeing the importance of automation. These producers are bringing in new Green-Field capacities. Intel is building a $20 billion facility in Ohio, and Texas Instruments has a facility coming on board next year. There is an interim incremental capacity that they’re able to improve and companies like us are engineering around the most acute shortages. So if there is a particular chip that we can’t get in the foreseeable future, we’re qualifying other suppliers and in some cases, we’re changing the designs of our products and it is an expensive, timely process.
So many companies are experiencing employee shortages. How do you attract employees, and what’s your secret to maintaining enough workforce?
We’re certainly not immune to the kinds of fluctuations that happen with workforce but I think that we’re winning more than we are losing. The first is the basics. You’ve got to have a competitive package of wages and benefits, and we have made a lot of investments in the last couple of years because in the past, we were typically dealing in more of a regional market. The vast majority of our employees were in Wisconsin and were in Ohio, and liked living in those places. So when somebody was trying to lure them away, it was typically a company that we knew well that was down the street. Today, with geography not being as much of a constraint. we can have a software developer who sits in Milwaukee working for Amazon. Who knows where that person’s boss sits. So we needed to make a change in terms of looking at our company that recognized that it wasn’t just the market reference points that HR used. We had to recognize that talent in hard to find jobs, we were gonna have to do more to make sure we were offering an acceptable experience. Other things like additional benefits, and more time off and vacation. Time off for volunteering and not stipulating where that person can volunteer. That all connects to the purpose of Rockwell and I think particularly for younger employees that we recognize have strong skills and are very mobile in terms of their jobs, connecting the purpose of Rockwell and what we do to help feed and clothe and keep the world safe is an important message. People care a lot more about culture now and we are an organization that is trying to create an environment where people can and want to do the best work. It’s not just about being able to do the best work, but you WANT to do the best work. Most of us in our careers have been in situations where we weren’t as highly motivated, whether it was with a boss that we didn’t like or a job where our heart wasn’t into it for whatever reason. So we say this is what we are trying to get done in terms of earning the longevity of the employees at our company.
What types of things is Rockwell Automation doing to incorporate diversion, inclusion, and accessibility in your employees so that you can have a more attainable and sustainable employee base?
We made a statement recently that diversity in all its forms is good for us. Because diverse teams make better business decisions. It diverse points of view, ethnic, gender, and diversity in all its ways. We’re committed that because we believe that it reduces the risk of creating a tunnel vision. If all of us came from the exact same background, it’s gonna be harder to be accepting of different points of view and act with the agility we need to. So we have said that openly and we’ve set out to make that a reality. That has helped us move at a faster pace than we might have otherwise without a commitment to new ideas from all over. It’s a fundamental part of our culture.
What do you think is coming faster at us than what we think is coming at us?
Chips, talent, and the war in Ukraine. Chips are clear and present. I’m dealing with those every day. Talent we talked about. We’re relatively less impacted by the war in Ukraine. That could go lots of different ways. And also, China. The chip shortage and what we’re dealing with now would be probably somewhat tame compared to hostilities that could shut down the capabilities in Taiwan if China did something there because the biggest manufactures of the fundamental wafers which semi-conductors are made are largely in that area.
In relation to the talent shortage, the people who understand what goes on in plants are retiring. We’re not seeing that as an exciting vocation or skill for people who are coming out of college. You don’t need a four-year degree to be very successful in these opportunities. And that’s why we’ve extended our programs like returning veterans, and other people who may not have been interested in manufacturing, but there’s a huge opportunity to have a successful career there. That’s not just in the plants, it’s also in our development.
Stay on the lookout for more content being available soon if you weren’t able to attend our Outreach event. Please check out our News & Events section for upcoming networking events in the area.